Development Support Services
If you have any trouble woth developing a new product, our balancing technology and rotary machine vibration evaluation technology will help you.
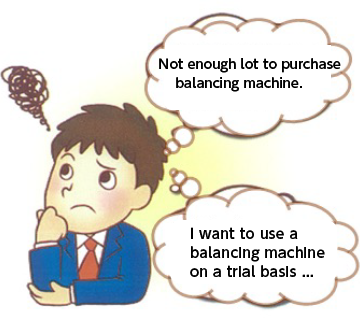
Balancing Services
The vibration problem of rotating parts is mostly due to unbalance.
We propose, experiment, and measure balancing of newly developed products.
We also design and manufacture attachments for rotors with complicated shapes and new workpieces.
Rotating Machinery Vibration
Please feel free to contact us if you have any problems with the vibration of the rotating machine, or any inquiries.
Qualified personnel for IS018436-2 Condition monitoring and diagnostics of machines (Vibration); Category II: 28, Category III: 12, Category IV: 1
Balancing
(1) Horizontal balancing machines
This type of machines is capable of measuring ultra-small to medium-sized rotors. Not only rigid rotors, but also elastic rotors and magnetized rotors can be balanced. If the rotor shape is complicated, we can design and manufacture a special attachment.
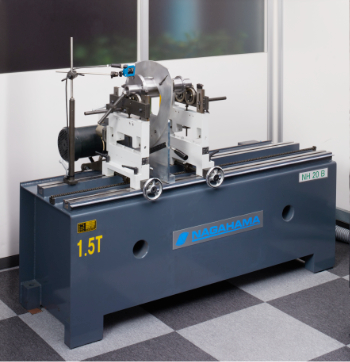
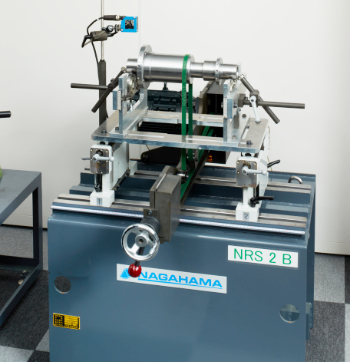
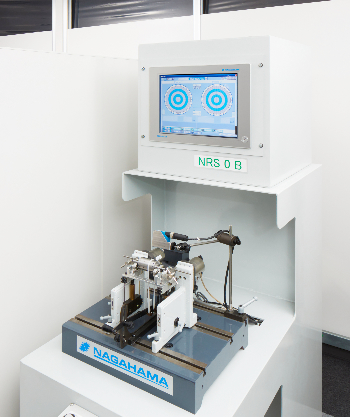
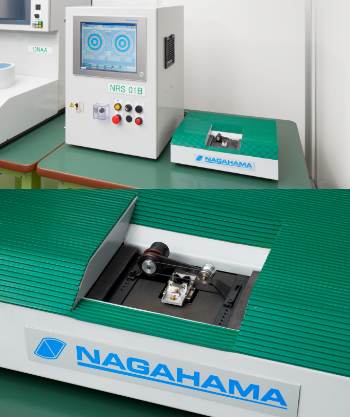
Model | Type | Number of balancing planes | Max. diameter [mm] (reference value) | Mass range[kg] (reference value) | Shaft diameter range[mm] | Bed length [mm] |
---|---|---|---|---|---|---|
NH20B | Hard | 2 | 800 | 10 to 40 | 8 to 140 | 1500 |
NRS2B | Soft | 2 | 180 | 5 to 20 | 8 to 140 | 750 |
NRS0B | Soft | 2 | 100 | 0.1 to 2.5 | 5 to 30 | 360 |
NRI01B | Soft | 2 | 10 | 0.001 to 0.04 | 2 to 3 | – |
* For NRS and NRI types, it is usually necessary to design and manufacture a special attachment to fit the rotor.
(2) Vertical balancing machine
The vertical balancing machine can also measure the unbalance of a rotor without a shaft. Normally, it is necessary to design and manufacture a special attachment to fit the rotor.
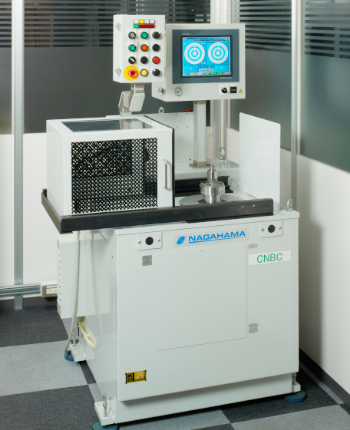
Model | Type | Number of balancing planes | Max. diameter [mm] (reference value) | Mass range [kg] (reference value) |
---|---|---|---|---|
120CNBC | Soft | 2 | 450 | 1 to 8 |
(3) Balancing of elastic rotors
Balancing can be performed at the specified speed as long as it is within the speed range applicable to the balancing machine. We can also provide field balancing service for actual rotating machineries. The efficiency of balancing of an elastic rotor depends on the number of critical speeds considered and the position and number of balancing planes, but we can provide best solution for balancing using optimal computation.
Solution to the vibration problem of rotating machines
We provide support for investigation methods, investigation of causes, and countermeasures for vibration problems of newly developed or existing rotating machines.
As professionals in vibration problems, we will help and solve your problems with our research experience on those problems of rotating machinery.
Typical vibration evaluation ways are as follows.
(1) Shaft vibration analysis
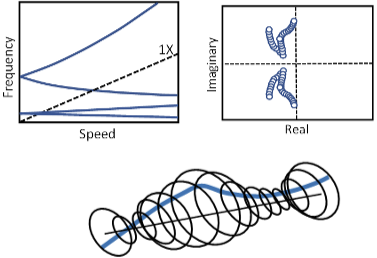
It is possible to evaluate the natural frequency characteristics of bending vibration by creating a shaft vibration analysis model from detailed information on the rotor and bearings.
We can evaluate critical speeds with Campbell diagrams, stability evaluations with root locus plots, and evaluation of unbalance responses and static deflection.
Evaluation of torsional vibration characteristic for single or multi axis rotor is also available.
(2) Measurement and analysis of shaft vibration
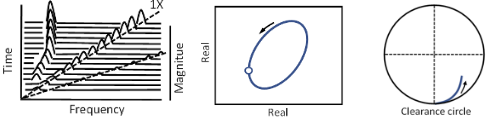
This is a method to grasp the state of the actual rotating machine in detail from the information such as the dominant frequencies of shaft vibration, orbit (dynamic motion of shaft center), and shaft center (static position of shaft center in the bearing clearance).
(3) Torsional vibration measurement
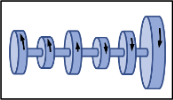
This method uses an encoder or zebra tape to sample rotational pulse signals with an equal angle pitch at high speed and evaluate the torsional vibration of the rotor.
Understanding the resonant speed is especially important in reciprocating machines, because resonant amplitude of torsional vibrations causes many problems.
(4) Experimental Modal Analysis (EMA)
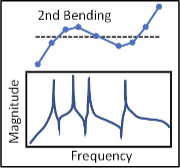
The natural frequency, natural mode, and mode damping ratio, which are the natural vibration characteristics of the bending vibration of the rotor, can be found by the excitation test in stand still condition.
The accuracy of the rotor shaft vibration analysis model can be evaluated and improved by conducting the test in the free support condition to eliminate uncertainties such as bearing stiffness.
Information on the unique mode of a machine is a very effective means when changing the structure of a general machine structure for the purpose of avoiding resonance.
In addition to the above, ODS analysis(Operational Deflection Shape)that evaluates the forced vibration mode of a machine in operation, and OMA analysis (Operational Modal Analysis)that obtains the natural frequency characteristics only from the vibration response of a machine that is difficult to stop or vibrate are also available.